When it comes to sandblasting and other high-demand industrial processes, precise control and reliability in airflow management are critical. While Variable Air Volume (VAV) valves are typically associated with HVAC systems, they can also be adapted for specialized applications like sandblasting. However, in such environments, the standard valve configuration often isn’t sufficient. Instead, a modified setup is necessary to handle the unique demands of these operations, especially when it comes to pressure control, leakage prevention, and durability.
Key Differences in VAV Valve Configuration for Sandblasting
VAV air valves used for sandblasting and similar industrial tasks, typically sized at 3/4″ or 1″, undergo several important modifications compared to conventional usage. These changes are specifically designed to manage high-pressure air delivery and to minimize or eliminate air leakage under reverse flow conditions.
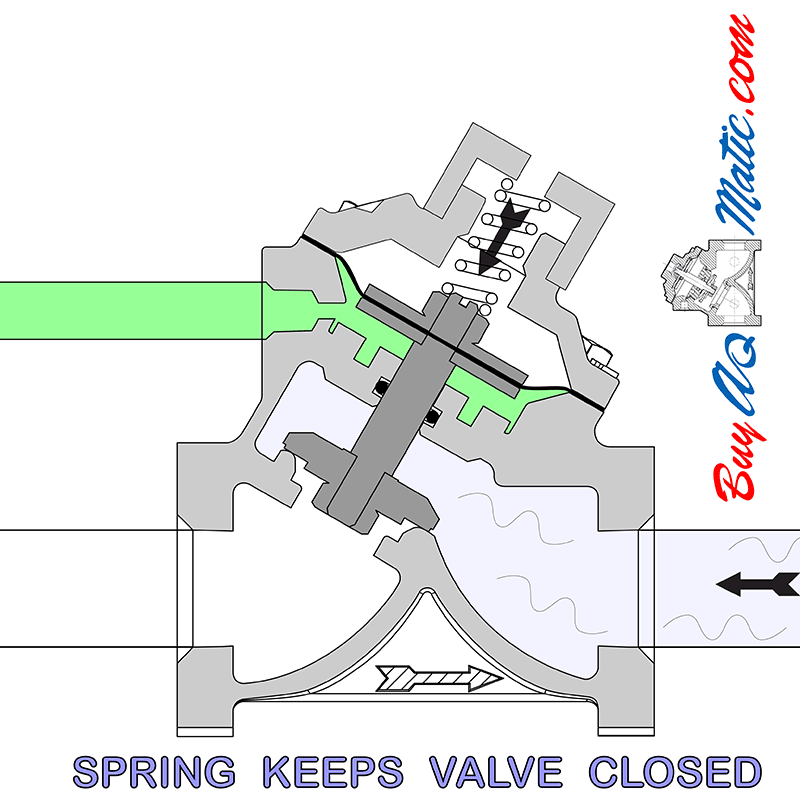
1. Reversed Flow Configuration
One of the most significant adjustments involves the direction of airflow. In these applications, the valve is used in a reversed configuration, meaning the airflow is directed opposite to the direction indicated by the valve’s stamped flow arrow. This reversal is not arbitrary; it takes advantage of the internal valve structure to better withstand the sudden surges and pressure variations common in sandblasting.
2. Spring-Assist Closed Configuration
To ensure a tight seal and prevent leakage, a spring-assist closed configuration is installed on the valve cap. This mechanism adds a mechanical force that helps the valve remain securely closed when needed, mainly when the air supply is off or fluctuating. This added pressure from the spring aids in preventing backflow and leakage, especially critical when abrasive materials or high-pressure air are involved.
3. Modified Control Pressure Application
In a typical valve, the side port usually functions as a vent. However, control pressure is applied to this side port in this specialized configuration. By repurposing the vent port for control pressure, the system allows for better management of valve operation, enabling quick and precise responses to control signals, which are essential in processes where exact timing and control of airflow are necessary.
4. Plug Removal for Enhanced Functionality
Notably, the plug that is normally added to the top of the valve is not included in this setup. This omission is intentional and part of the design strategy to accommodate the reversed airflow and the spring-assisted closure. Leaving out the plug prevents interference with the modified airflow path and ensures the valve operates smoothly under these altered conditions.
Why These Modifications Matter
In sandblasting, even a tiny amount of uncontrolled air leakage can lead to inefficiencies, safety concerns, or damage to materials. These valve modifications aim to prevent those issues by creating a system that maintains tight control over high-pressure air delivery and shuts off securely when not in use.
Furthermore, reversing the flow and applying control pressure to the side vent allows for faster actuation and better responsiveness, which can be crucial in timing-sensitive processes.
Conclusion
While VAV valves are not traditionally designed for sandblasting applications, they can serve reliably in these high-performance environments with a few key adjustments. By reversing airflow, applying a spring-assist closure, reconfiguring control pressure ports, and removing the standard top plug, these valves become well-suited to handle the demands of sandblasting and similar industrial processes. When properly configured, they provide consistent performance, tight control, and minimal leakage, critical factors for success in high-pressure air applications.